製造1課の課長を務める持田は2000年に入社。入社当初から一貫して、製造部門において技術者として業務をおこなってきました。
製造1課は、社内でも比較的若い技術者が多く、持田が中心となって課をまとめています。製造している製品や、加工技術の特長、製造で気を付けている点などを聞きました。
切削加工からホーニング・ラップ研磨、検査まで一貫生産
製造1課では、CNC自動旋盤、平面ラップ盤、内径ホーニング機などを用いて、様々な部品の製造をおこなっています。
持田
「加工している製品は各種あります。特に多く加工している製品は、エンジンに使うシートバルブです。シートバブルだけで幾つかの品番があり、月の生産量は数万個にもなります。元材から切削加工、熱処理、ホーニング加工、ラップ加工をおこない、全数自動測定器により精度を管理しながら製造します。製造後、洗浄処理をおこない、最後に検査部門において目視で全数検査をおこなって完成です。」
シートバルブは、エンジンへの燃料供給のための部品です。気密性が重要となるため、非常に厳しい加工精度が要求されます。量産も求められるので、コストを上げないためにも、加工条件を追い込まなければなりません。安定した製造の維持には、加工装置の微細な調整も必要となります。
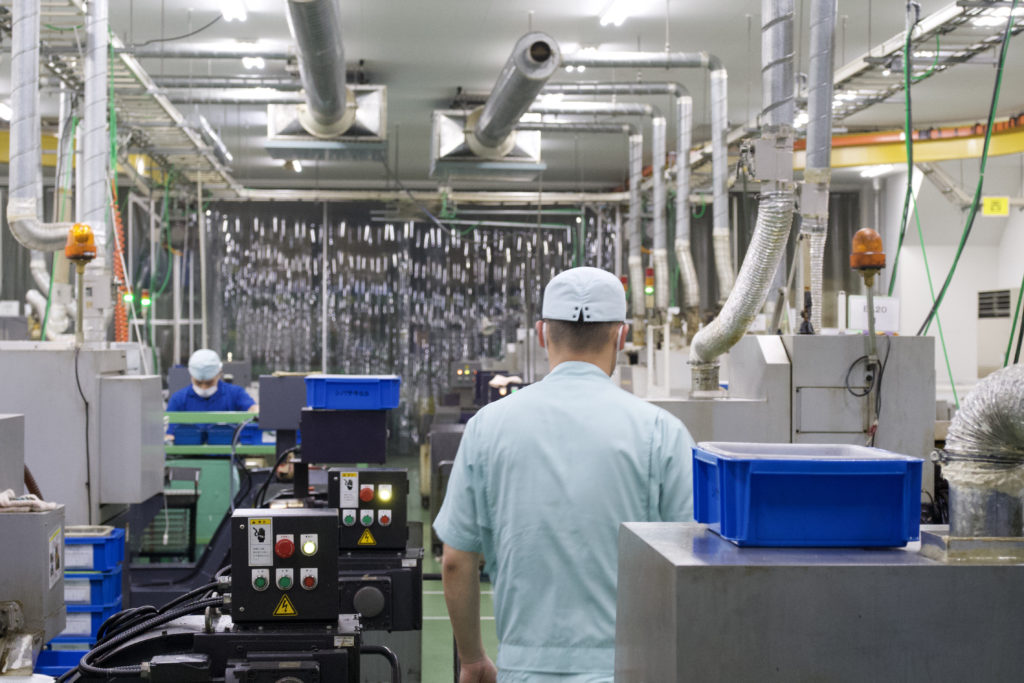
持田
「素材はSUS304、SUS420、SUS440などのステンレス材を扱うことが多いですが、鉄、アルミ、銅、真鍮など各種取り扱っています。難削材なども、工具の選定や加工工程の調整などをおこない対応していきます。今まで最小のものだと、φ2程度の径の部品まで対応しました。工場は24時間製造に対応可能で、キャパシティもありますので、かなりの数の量産品にも対応できます。専用に設計された耐熱ナイロンコーティングトレイを使用して並べ替えの手間を削減するなど、コストダウンにも努めています。」
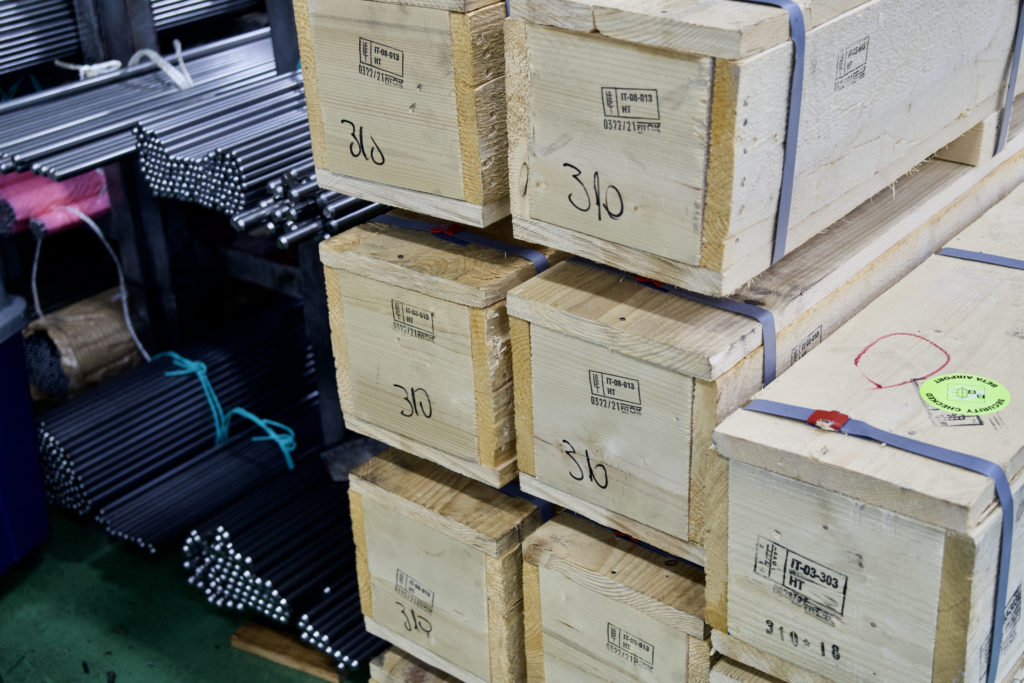
写真:ステンレスをはじめ、海外からの輸入材など様々な材質を加工している。
5μの精度の量産加工を実現する、技術者の経験と知恵
高品質製品を適正コストで量産化するには、作業の手間を減らしてコストカットをおこなうだけでは足りません。高い精度を保ったまま、加工そのものの効率を上げる必要があります。
持田
「お客様からいただく図面の寸法精度は、年々厳しくなっています。どうやったらその精度を出せるか、加工条件を常に考えながらやっています。例えば、シートバルブならば、穴の精度をだすためのホーニング加工は2回でおこなうのが一般的です。当社では、工程や機械の加工条件、使用する工具などを工夫することで、1回のホーニング加工で5μの精度を出しています。加工の手間が1つ減ることでコストダウンできるのです。」
最適な加工条件は、技術者がそれぞれ経験や知恵を持ち寄り、他からの助けも受けることで導き出されます。また、最適と思っていたものも、時間の流れとともに変化していくので、常にアップデートしていかなければなりません。
持田
「条件出しは、技術者が経験、知恵を持ち寄ってやっていますが、結構かかりますね。条件が決まり、量産加工をやっていると工具の摩耗などで条件が変わってきます。加工機も調整により精度に影響が出るので、これは経験で学んでいくしかありません。工具も年々いいものが出てきます。工具メーカーと直接やりとりして要望を伝え、より最適なものを出してもらうこともあります。社内、社外のどちらもコミュニケーションは大切です。」
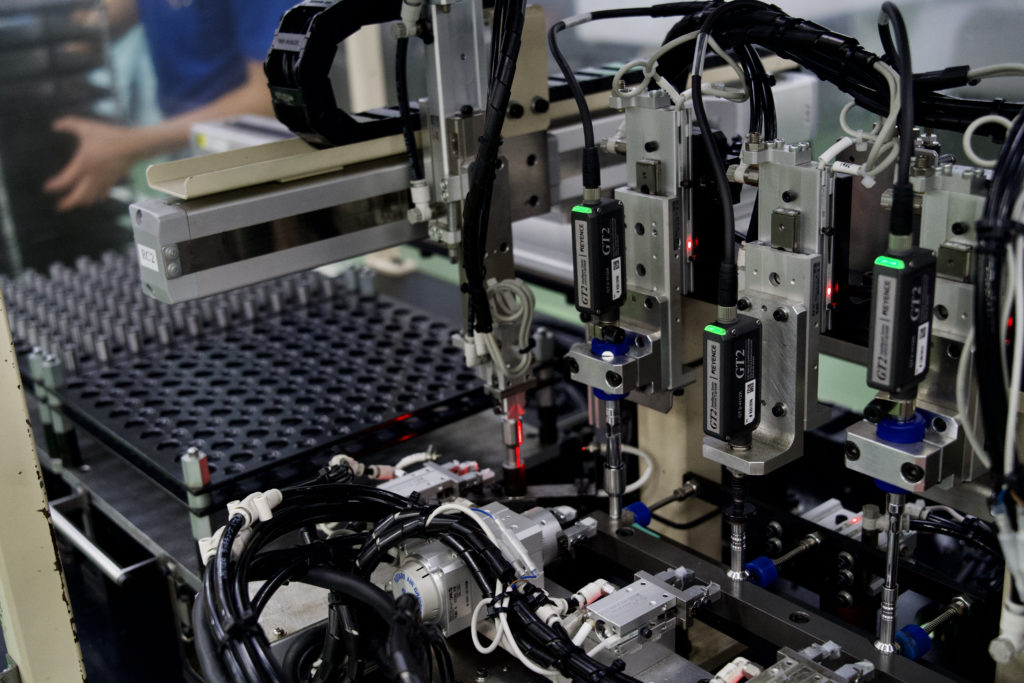
現場と検査部門とで管理される加工精度
高品質を維持するためには、加工機の管理はもちろん、検査による精度管理も欠かせません。シバサキ製作所では、加工工程での全数自動測定器による検査に加え、検査部門での全数検査もおこなっています。
持田
「品質管理という点では、不具合品をお客様に流さないのが第一です。製造における不良率が高ければ、流出する可能性も高くなるので、検査での不良率も集計するようにしています。加工工程での不良率と、検査部門での不良率との両方を把握してゆきます。」
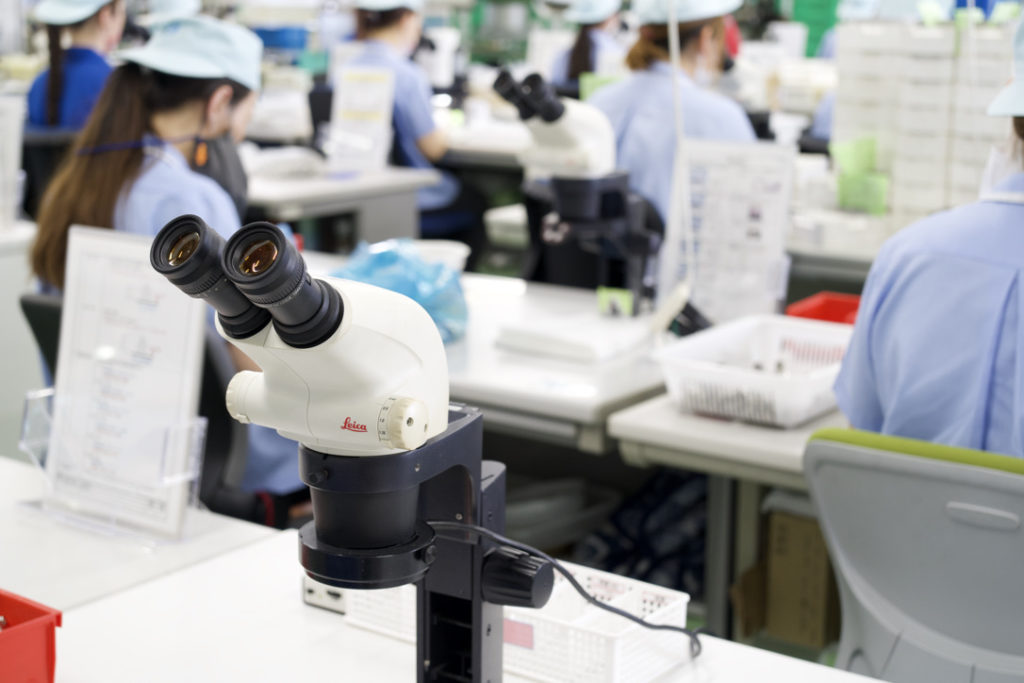
写真:高精度の実体顕微鏡を使用した全数検査ライン。
品質管理では、部門間のコミュニケーションも欠かすことはできません。
持田
「加工工程での不良率は、自分たちで把握していますが、検査部門での不良率に関しても状況を共有しています。また、検査部門でこういう問題が起こっている、こういう不良が最近多いといった異常を、現場の技術者に伝えるためのシステムがあります。部門間でコミュニケーションをしっかりとり、不良率を減らすことでもコストダウンに努めています。」
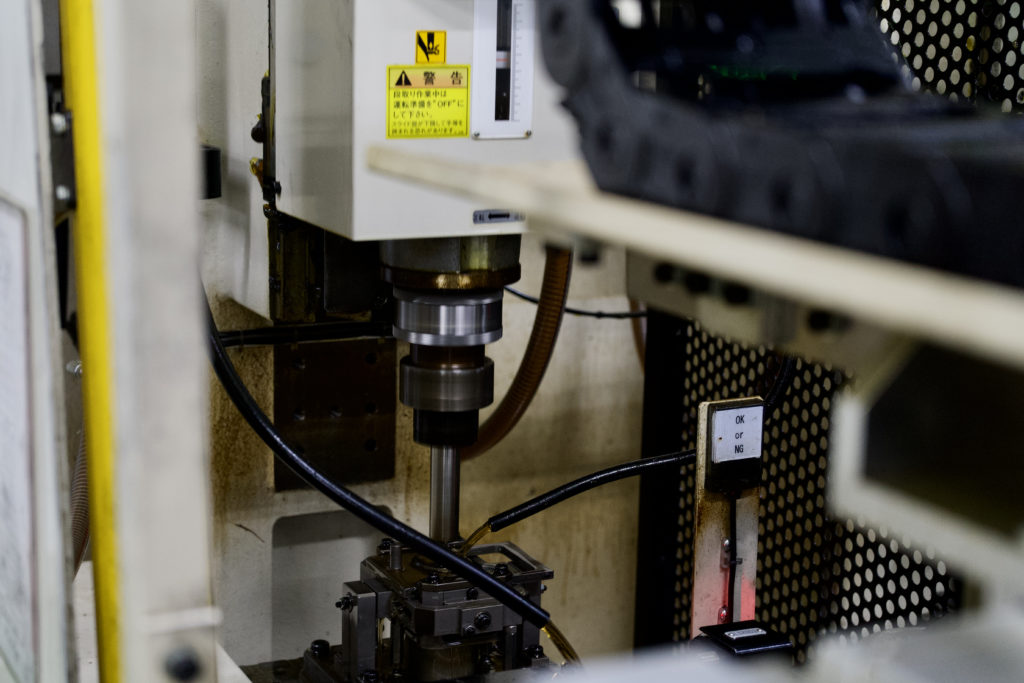
写真:内径をμの精度で仕上げるホーニング工程
新たな分野への挑戦も
最後に今後の展望について聞きました。
持田
「精密加工を長くやっていますので、自動車部品に限らず、医療や化学、半導体など、様々な分野の加工に取り組んでいきたいと思っています。今以上に精度が厳しい加工に挑戦をしていきたいです。
よくQCD(Quality:品質、Cost:コスト、Delivery:納期))と言われます。コストの面では、加工工程や工具、手順などを改善していくことで、こたえることができます。品質と納期に関しては、どちらも悪くなれば、お客様に直接迷惑がかかってしまいます。品質面としては、まずは不良品を出さない体制を作ること。納期についても、品質が崩れだすと影響がでてきます。品質が安定すれば納期にもこたえられるので、改善にとりくむ流れを止めないというのが大切です。今後も社内外の連携をうまく取りながら進めていきます。」
ー 以上 ー
インタビューとコラムのライティング:馬場吉成
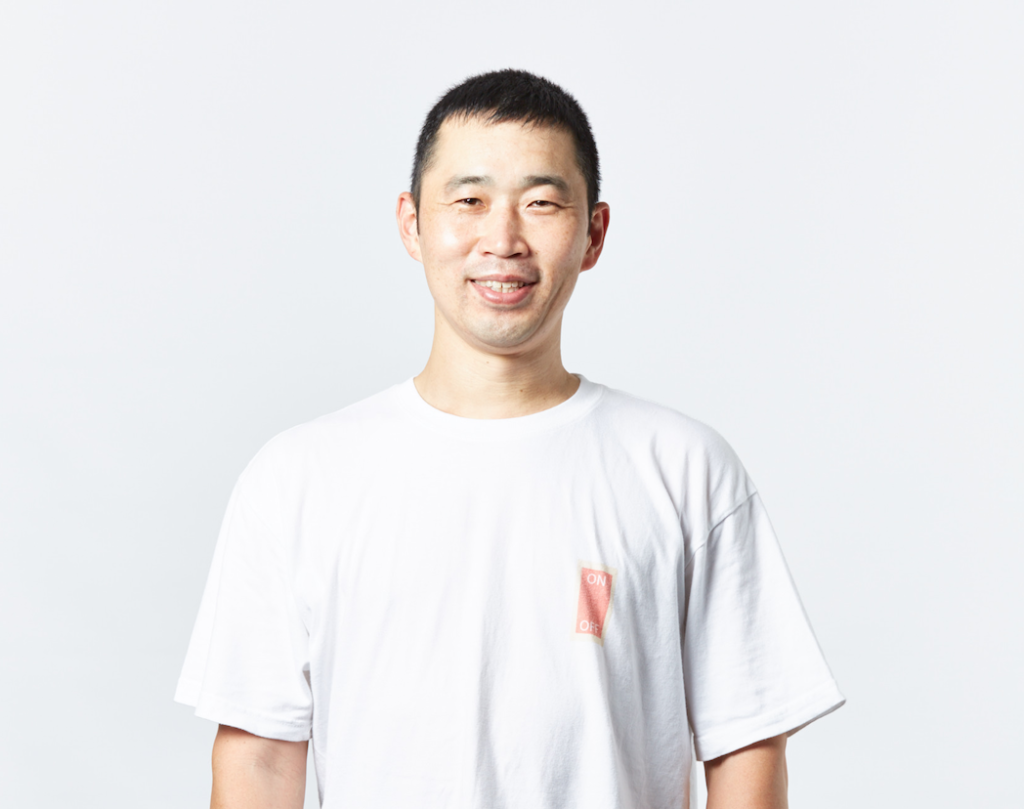
工業製造業系ライター。機械設計の業務を長く経験。元メカエンジニアで製造の現場を直接知るライターとして製造業向け記事、テクノロジー関係の記事を多数執筆。http://by-w.info/